Courses, News
Robotic Ecotectonics
Description
Climate change is challenging humanity. There is an increasing need to develop sustainable building systems for zero or negative carbon emissions. Innovation in ecologically sound materials and sustainable construction techniques could revolutionize the building industry, which in turn could enable the rapid construction of building envelopes using local and low-carbon materials. Robotic additive manufacturing’s versatility can be used to construct complex adaptive envelopes that actively support local ecosystems.
This course challenges traditional linear construction methods by introducing a circular economy approach. The “reduce-reuse-recycle” strategy promises a way to decrease embodied carbon emissions in building sectors. The research will explore the possibility of developing ecological tectonic (ecotectonic) constructions. Ecotectonic construction, which considers multispecies design, moves beyond anthropocentric tectonics. It combines upcycling waste materials with robotic 3D printing to reduce the negative impacts of building envelopes.
Students will design and construct eco-composite envelopes, which may include features to capture carbon, block heat radiation, or serve as an acoustic system. To promote sustainable construction, this studio will apply innovative methods to reuse recyclable plastic waste or repurpose local soil mixed with agricultural by-products. Repurposing these unconventional materials requires analyzing their characteristics and the use of additives to make them suitable for 3D printing. Robotic additive construction enables the addition of layers based on performance needs. Different layers—like green cover, insulation, and structural layers—can be 3D printed together to foster a proper ecology to maintain the structure as a living organism.
Students will explore the design-to-fabrication process by developing prototypes to evaluate each phase through an ecologically active material system, computational design, and robotic additive construction. Students will produce detailed drawings of a façade or envelope system, conceptual drawings of the implementation of this system on a building scale, and a 3D printed full-scale mock-up of the ecological envelope system.
Image Credit
E. Baharlou, University of Virginia, 2021.
Courses, News
Additive Tectonics
“When a structural concept has found its implementation through construction, the visual result will affect us through certain expressive qualities which clearly have something to do with the play of forces and corresponding arrangement of parts in the building, yet cannot be described in terms of construction and structure alone. For these qualities, which are expressive of a relation of form to force, the term tectonic should be reserved.”
— Eduard F. Sekler (1960), “Structure, Construction, Tectonics”, in Structure in Art and in Science.
Description
Advances in computational design methods and fabrication techniques provide new possibilities for architectural designers to consider different paradigms for design and making. These paradigms emphasize the relationship between formation and materialization. Through robotic additive manufacturing, designers can construct buildings or building elements quickly.
The studio “Additive Tectonics” explored the tectonic expression of additive manufacturing in different architectural contexts, from constructing affordable housing with earth materials to investigating the construction of settlements on other planets. The studio focused on the exploration of such architectural tectonics as an abstracted skin or wall system; a tower or a column as a structural element; a vault or a shell as a roof system; a hut or a shed; or other, new building tectonics. One-to-one structures were designed for the North Terrace at the University of Virginia’s Campbell Hall.
Students explored additive tectonics through three stages. The material system development stage demonstrated various materials—such as bio-based, bio-degradable, or bioplastic materials—and their properties and limitations in additive manufacturing. In computational design development, students considered the material properties and fabrication constraints in prototyping. Finally, robotic additive construction—which can be defined as abstraction, formation, rationalization, and materialization to explore novel tectonics—enabled students to execute their design prototype to examine their design’s tectonic potential in building an architectural element.
A series of integrative workshops supported this studio. Formation workshops introduced Grasshopper as a CAD software that can be used for form generation. Materialization workshops presented students with a numerical-based fabrication process. Students learned to control an industrial robotic arm and 3D-print tectonic prototypes.
Image Credit
E. Baharlou, University of Virginia, 2021.
Courses, News
Design Computation 1
Description
Computation has a profound impact on a contemporary understanding of architectural form, space, and structure. It shifts the way one perceives form, the way in which form is purposed, and the way in which form is produced. The course “Design Computation 1” introduced students to the fundamentals of computational design and computational design thinking in architecture. The course examined the potential of algorithmic logic to generate spatial structures by analyzing and abstracting architectural geometry.
In addition, this course introduced students to the principles of computational formation processes that incorporate observation, translation, abstraction, and generation. It also equipped students with computational skills to use the power of computation as not only a representational tool but also a generative one.
The course had three stages. Phase one introduced students to the basics of visual programming and geometric logic. The second phase examined the add-ons developed for the Grasshopper plug-in to Rhino to explore the processes from formation to materialization. Selected add-ons supported the generation, simulation, visualization, and fabrication of forms. Phase three explored parametric and algorithmic geometry through a series of examples to introduce students to architectural computation logics. Each session consisted of a seminar and exercises to assist students with computational design and thinking.
Image Credit
C. Geiger, J. Hirschlein, and N. Lindemann, ICD, University of Stuttgart, 2016.
Selected Project
Generative Crossed Timber System
Description
The project “Generative Crossed Timber System” creates an open-ended timber system that can form different architectural elements by applying the notion of generative design, the materiality of wood, and digital fabrication. This project was named the best in student design in Fast Company’s 2022 Innovation by Design Awards.
Project Development
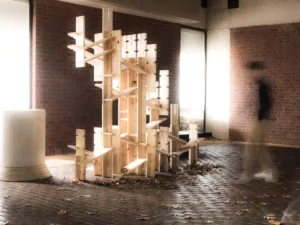
© C. MacDonnell, Z. Shen, Y. Zhou, 2021.
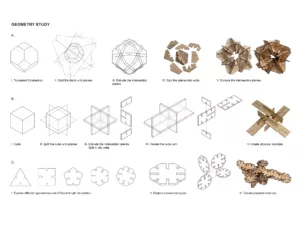
© C. MacDonnell, Z. Shen, Y. Zhou, 2021.
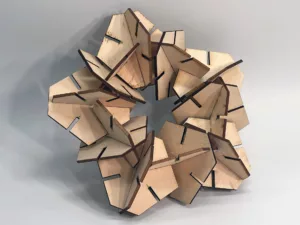
© C. MacDonnell, Z. Shen, Y. Zhou, 2021.

© C. MacDonnell, Z. Shen, Y. Zhou, 2021.
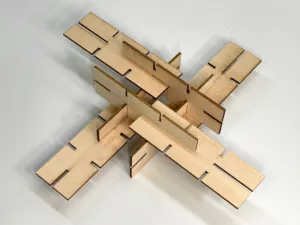
© C. MacDonnell, Z. Shen, Y. Zhou, 2021.
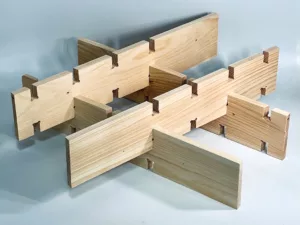
© C. MacDonnell, Z. Shen, Y. Zhou, 2021.
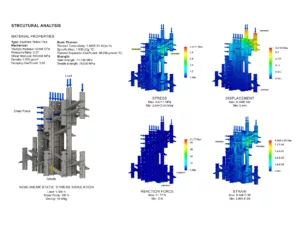
© C. MacDonnell, Z. Shen, Y. Zhou, 2021.
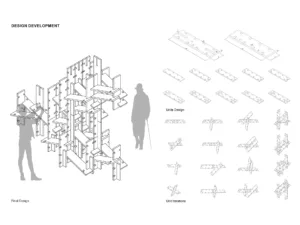
© C. MacDonnell, Z. Shen, Y. Zhou, 2021.
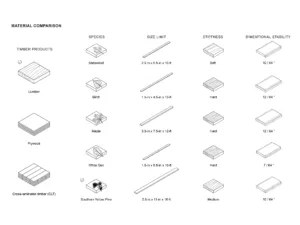
© C. MacDonnell, Z. Shen, Y. Zhou, 2021.
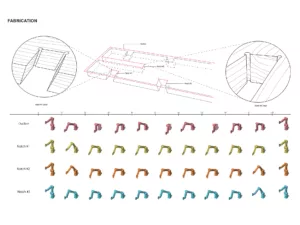
© C. MacDonnell, Z. Shen, Y. Zhou, 2021.
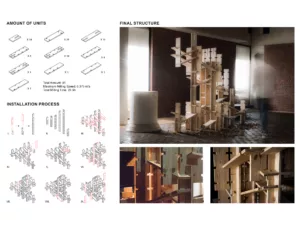
© C. MacDonnell, Z. Shen, Y. Zhou, 2021.
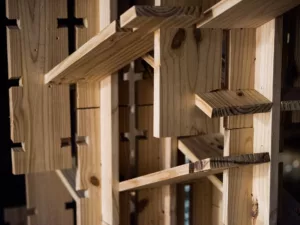
© C. MacDonnell, Z. Shen, Y. Zhou, 2021.
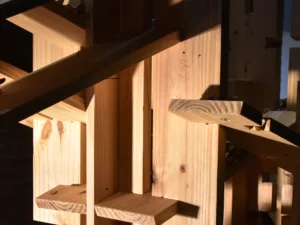
© C. MacDonnell, Z. Shen, Y. Zhou, 2021.
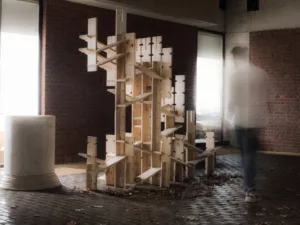
© C. MacDonnell, Z. Shen, Y. Zhou, 2021.
A cross-referencing method—which includes geometry study, material study, fabrication tests, and structural analysis—was developed by this research collective to serve as the driving force of this project. The feedback among each approach provides guidelines for future research and practice. The geometry study shaped the form-searching process and provided theoretical support for the unit design. It provided greater understanding of the physical properties of different geometries and connection methods. The material study focused on material dimension, grain orientation, stiffness, and elastic properties.
Three key elements of the final design came from the fabrication test: 1) the milling speed of the current robot setup limits the scale of final structure, 2) the dimension limitation and maximum load of the robot affects the form and size of the unit, and 3) the accuracy of the robotic fabrication and the bending behavior of wood material during the change of air humidity required more tolerance to be considered during the unit design process. The final design was also guided by the feedback of the structural analysis, which centered around the structural performance.
The final form consists of 81 pieces of pine lumber that are only connected by notches of different dimensions. The single size of each piece is 1”x 7” x 28”. The column-like structure can be re-formed to other architectural elements by rearranging the units and can be extended to other scales by aggregating through the opened notches.
Author and Image Credit
Chris MacDonnell, Ziwei Shen, Yuwen Zhou.
Instructor
Ehsan Baharlou