Selected Project
Generative Crossed Timber System
Description
The project “Generative Crossed Timber System” creates an open-ended timber system that can form different architectural elements by applying the notion of generative design, the materiality of wood, and digital fabrication. This project was named the best in student design in Fast Company’s 2022 Innovation by Design Awards.
Project Development
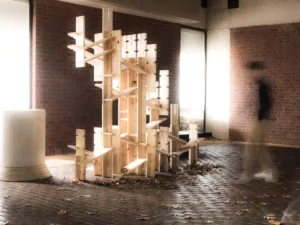
© C. MacDonnell, Z. Shen, Y. Zhou, 2021.
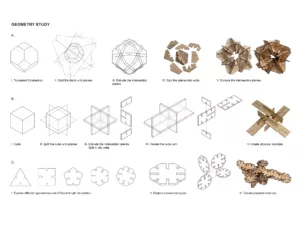
© C. MacDonnell, Z. Shen, Y. Zhou, 2021.
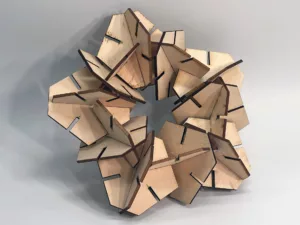
© C. MacDonnell, Z. Shen, Y. Zhou, 2021.

© C. MacDonnell, Z. Shen, Y. Zhou, 2021.
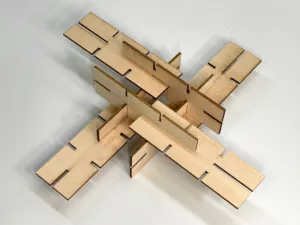
© C. MacDonnell, Z. Shen, Y. Zhou, 2021.
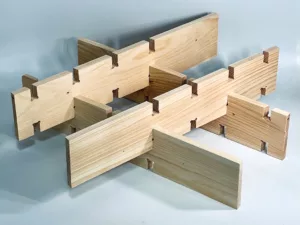
© C. MacDonnell, Z. Shen, Y. Zhou, 2021.
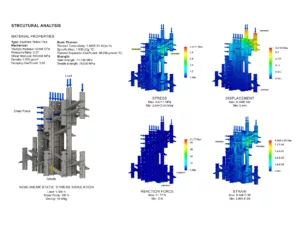
© C. MacDonnell, Z. Shen, Y. Zhou, 2021.
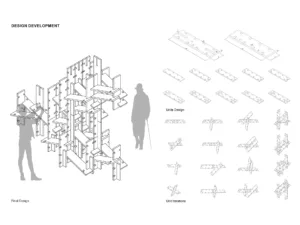
© C. MacDonnell, Z. Shen, Y. Zhou, 2021.
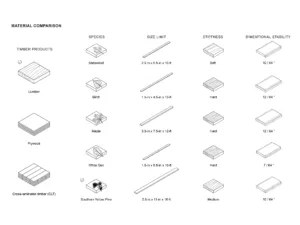
© C. MacDonnell, Z. Shen, Y. Zhou, 2021.
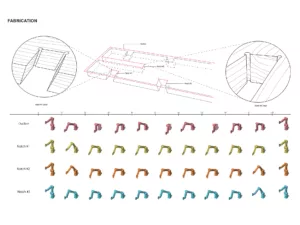
© C. MacDonnell, Z. Shen, Y. Zhou, 2021.
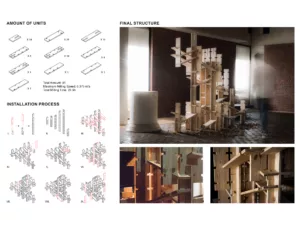
© C. MacDonnell, Z. Shen, Y. Zhou, 2021.
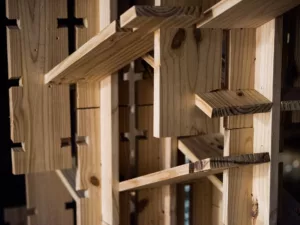
© C. MacDonnell, Z. Shen, Y. Zhou, 2021.
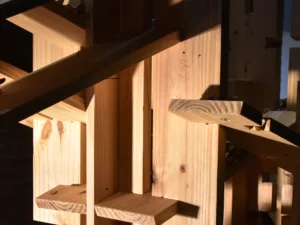
© C. MacDonnell, Z. Shen, Y. Zhou, 2021.
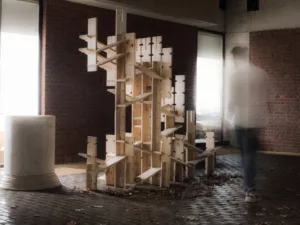
© C. MacDonnell, Z. Shen, Y. Zhou, 2021.
A cross-referencing method—which includes geometry study, material study, fabrication tests, and structural analysis—was developed by this research collective to serve as the driving force of this project. The feedback among each approach provides guidelines for future research and practice. The geometry study shaped the form-searching process and provided theoretical support for the unit design. It provided greater understanding of the physical properties of different geometries and connection methods. The material study focused on material dimension, grain orientation, stiffness, and elastic properties.
Three key elements of the final design came from the fabrication test: 1) the milling speed of the current robot setup limits the scale of final structure, 2) the dimension limitation and maximum load of the robot affects the form and size of the unit, and 3) the accuracy of the robotic fabrication and the bending behavior of wood material during the change of air humidity required more tolerance to be considered during the unit design process. The final design was also guided by the feedback of the structural analysis, which centered around the structural performance.
The final form consists of 81 pieces of pine lumber that are only connected by notches of different dimensions. The single size of each piece is 1”x 7” x 28”. The column-like structure can be re-formed to other architectural elements by rearranging the units and can be extended to other scales by aggregating through the opened notches.
Author and Image Credit
Chris MacDonnell, Ziwei Shen, Yuwen Zhou.
Instructor
Ehsan Baharlou
Selected Project
Robotic Serpentine Wall
Description
The project “Robotic Serpentine Wall” investigates new, unexpected uses of wood to construct an inhabitable structure. It created a structure that 1) celebrates steam bending’s ability to radically change wood’s structural potential; 2) is inhabitable, improves the site on which it was built, and is connected with the history of its larger context; and 3) was data- and mathematically driven.
Program Development
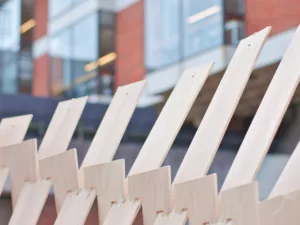
© L. Kirssin, B. Penny, T. Rhodes, (Photographer: Kwadwo Tenkorang), 2020.
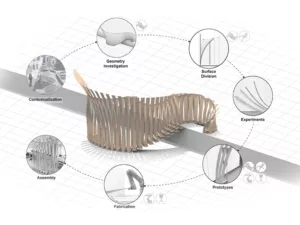
© L. Kirssin, B. Penny, T. Rhodes, 2020.
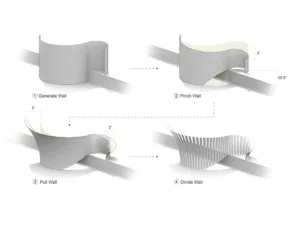
© L. Kirssin, B. Penny, T. Rhodes, 2020.
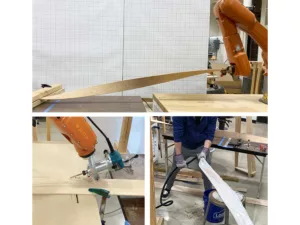
© L. Kirssin, B. Penny, T. Rhodes, 2020.
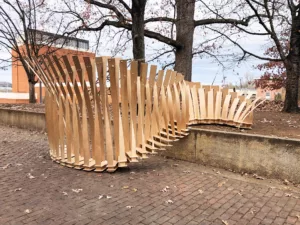
© L. Kirssin, B. Penny, T. Rhodes, (Photographer: Kwadwo Tenkorang), 2020.
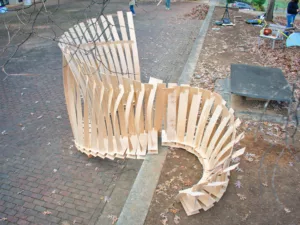
© L. Kirssin, B. Penny, T. Rhodes, (Photographer: Kwadwo Tenkorang), 2020.
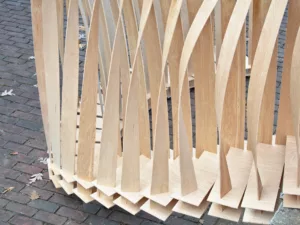
© L. Kirssin, B. Penny, T. Rhodes, (Photographer: Kwadwo Tenkorang), 2020.
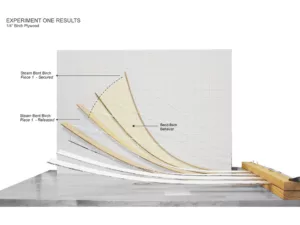
© L. Kirssin, B. Penny, T. Rhodes, 2020.
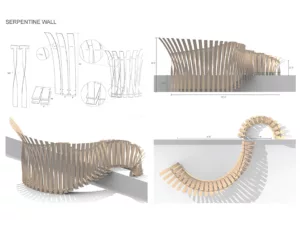
© L. Kirssin, B. Penny, T. Rhodes, 2020.
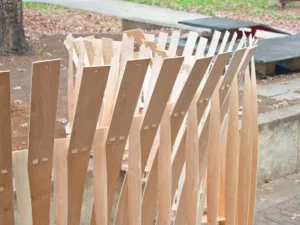
© L. Kirssin, B. Penny, T. Rhodes, (Photographer: Kwadwo Tenkorang), 2020.
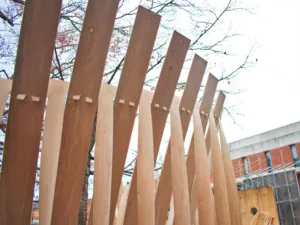
© L. Kirssin, B. Penny, T. Rhodes, (Photographer: Kwadwo Tenkorang), 2020.
This project responded to its site—the North Terrace of UVA’s School of Architecture—in two ways. First, it negotiated the step between the ground and the top of the planter box, a distance of 26 ½”, in a way that encourages small group interactions. Second, the form responds to the complex history of serpentine walls at UVA. This sinusoidal shape was manipulated to create a structure that produced a small gathering area on one side and a seat on the other. It was then reverse-engineered to minimize the number of unique components upon construction.
Several experiments were conducted to test the amount that pieces of birch plywood and oak plywood reverted to their original shape following steaming and either bending or twisting; birch plywood performed better in both. A third experiment determined plywood pieces needed to be a minimum length of 24” to prevent cracking as a result of twisting.
Prototyping the structure led to the discovery that the primary pieces work in tension, not compression. This in turn resulted in the inclusion of additional support pieces for greater structural stability.
The final design was constructed through a complex process of cutting, twisting and bending, and slotting the pieces together. Each piece was machine cut according to the specific measurements dictated by the digital design. They were then steamed before being twisted and bent into position, allowed to dry, and put together. The final assembly process revealed that the connections between wall sections were necessary for the structure to be free-standing.
This project was awarded the 2021 Bruce Abbey Technology Award. It was featured on the University of Virginia School of Architecture’s website.
Author and Image Credit
Leah Kirssin, Bay Penny, Trenton Rhodes.
Instructor
Ehsan Baharlou